About Front Range Woodturners
We are the Denver area chapter of the AAW (American Association of Woodturners) serving woodturners throughout Colorado’s Front Range.
Our Meetings
We meet on the first Tuesday of every month from 6:15 PM to 9:00 PM in the basement of Rockler Woodworking and Hardware, 2553 S Colorado Blvd, Denver, 80222.
Visitors are welcome to join us at one of our meetings to see what we are all about.
Upcoming Demonstrations
July – Josh Buettner – Bent Branch Vase
In this unique demonstration, Josh Buettner shares his journey and techniques for creating “Bent Branch” Bud Vases—a form he first encountered through an online symposium with woodturner Paul Russel in early 2023. Since then, Josh has crafted over a dozen of these striking pieces using a variety of wood species including black walnut, cottonwood, ash, honey locust, elm, and his personal favorite, a Russian olive burl gifted by a friend.
Each vase begins with a naturally bent or crooked branch, allowing Josh to blend refined turning on one side with the organic, live edge beauty of the wood on the other. While the concept may seem straightforward, the process involves a significant amount of interrupted cuts, requiring precision and practice to execute safely and effectively.
Josh describes this project as ideal for intermediate to advanced turners due to its technical demands and safety considerations—but encourages curious novices to approach with care, noting that he himself was a beginner when he first took it on.
Aug – Kirk DeHeer – Bowl Turning 101
With over 25 years of experience, Kirk has an extensive knowledge of woodturning tools, equipment and techniques. Kirk has been a resident instructor at Craft Supplies USA in the Dale L. Nish School of Woodturning for more than 15 years.
This demo will help woodturners / makers create bowls that maximize the available time by turning a bowl that is aesthetically pleasing, thus being more desirable to you. Kirk is also teaching a Bowl Turning 101 class the following day.
Kirk will demo the process of turning a bowl beginning with a dry bowl blank. He will break down the turning and finishing process so that it is easy to understand. Throughout the demo emphasis is placed on how to make efficient cuts that produce great results. In addition, proper tool use, chucking the bowl while turning, and recommended methods of sanding and finishing are thoroughly covered. As always, proper sharpening techniques are covered as well. Sharp, properly ground tools are one of the keys to success in all woodturning. By learning the fundamentals of bowl turning, you too can create beautiful, functional bowls that you can enjoy every day!
Topics covered:
- Safety.
- Elements of good design.
- Tool selection.
- Proper tooling techniques.
- Chucking methods.
- Turn a bowl that is designed to feel good in the hand.
Demonstrators scheduled for 2025:
Sep – Raleigh Lockhart – Nested Lidded Box
Oct – Cindy Drozda – Banksia Pod Ornament (IRD)
Nov – (Heather has to reschedule) Heather Marusiak (AAW’s Professional Outreach Program (POP) 2024 POP Showcase Artist) – Texture and Color
Dec – Holiday Party
Member Benefits
- Library – The Front Range Woodturners has an extensive collection of books, magazines, and videos available for members to check out at no cost.
- Demonstrations – Monthly meetings feature an exciting demo given by one of our club members or a professional turner. When available we also offer a full day hands-on class with these renowned turners at a nominal cost.
- Brown Bag Demo – Bring your lunch and watch a free in-person mini demo on a variety of topics in a smaller, more relaxed setting.
- Wood Drawing – Members can bring some of their excess (good) wood to a meeting so it can find a new home with a different member. You can never have too much wood!
- Group Buy – Do you want to save money? We have vendor discounts with Internet suppliers, local suppliers, tool and steel suppliers and wood suppliers. Through our deals with these vendors our members can easily earn back the cost of membership!
- Ladies of the Lathe – All female members of the FRW, aged 18 or older, are invited to join the Ladies of the Lathe. LOTL is intended to provide a comfortable, easy-paced, and non-threatening environment for women to learn and advance their skills in turning.
- Mentoring – Members have access to several programs to help increase their woodturning skills. Group sessions are held monthly and one-on-one mentoring on various topics can be arranged with experienced FRW volunteers.
- PHEOG – The Pete Holtus Educational Opportunity Grant program provides grant money to members through an application process. Applicants may request money for woodturning related classes, workshops, or symposium fees.
- Workshop Tours – monthly tour of members workshop. Get ideas and get inspired!
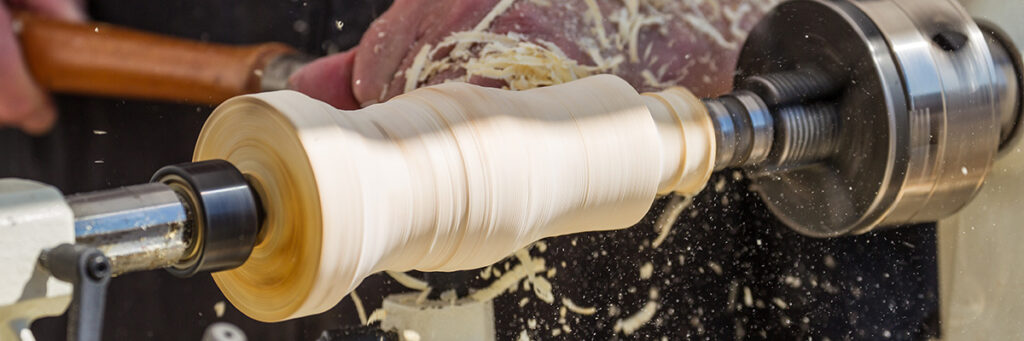
Special Notices
- The FORMS tab (above) has all of our forms in one spot (Group Buy, Membership, Gallery, etc).
- The Turning Challenge for the August meeting is Make something from a Branch. Do you have an odd piece of wood you can’t figure out what to do with? Does it have a bend? How about a Bent Branch Vase like our July demonstration? Let you artistic imagination flow for this challenge.
- Our next Brown Bag Demo (“view and chew” as Raleigh said) is on July 8th. Rick Orr will demonstrate turning a small goblet (3.5″ tall by 1.5″ diameter). The goblet will include a captured and textured ring, some texturing on the goblet cup, and chatter work on the base.
- Our next Group Buy will be in July with pickup at the August meeting.
- TIME TO RENEW YOUR MEMBERSHIP. If you haven’t renewed by now you have been removed from the roster.
You can renew your 2025 membership using our online form if you want to pay with credit card or PayPal. If you want to pay with check you can fill out an eForm and mail it or bring to a meeting. Click on FRW Membership Info (top of the Home page), or the Forms tab and fill out the Current Member Renewal Online Form. - PHEOG Grant. Congratulations to the 2025 grant winners!
Marcee Morris
Don Sheffield
Brenda Blaesing
Rocky Mountain Folk School
(c/o Dennis Fanning)
Remember if you received an award you have 1 year to give your payback to the club.
Upcoming Events
- Summer BBQ !
Save the date! Our summer BBQ will be held on Sunday, July 20th, 2025 at the same park as last year. A SignUpGenius link has been sent to members of FRW and CWG.
The club will supply burgers, brats, dogs, chips, and drinks. Feel free to bring an appetizer, side, or dessert. If you can help with Set Up, Food Prep, or Clean up, it would be greatly appreciated!
- Set-up: 4-6 people to arrive by 10:00am to help set up canopies and move chairs & tables.
- Food Prep: 2 grill masters and 2 people to help cut and prep.
- Clean-up: 4-6 people to help pack and haul to parking lot.
RSVP by Friday July 11th.
- Tool sale / Swap Meet
Our annual Tool sale/swap meet is scheduled for Saturday Nov.1st starting at 11am.Do you have tools you no longer need? Do you have too much wood? Do you like to buy tools or wood? Do you want to put some cash in your pocket? Do you like to haggle and make deals? Then you’ve come to the right place! You can do any or all of the above at our annual swap meet and sale!
Upcoming Symposiums!
Rocky Mountain Woodturning Symposium
What a great Symposium! Mark your calendars for next year:
September 19-21, 2025
Loveland, CO
rmwoodturningsymposium.com/